Bagaimana mendesain bagian plastik
Deskripsi Singkat:
Untuk desain bagian plastikadalah untuk menentukan bentuk, ukuran dan presisi bagian, berdasarkan peran yang dimainkan bagian tersebut dalam produk, dan aturan proses pencetakan untuk plastik. Hasil akhir adalah gambar untuk pembuatan cetakan dan bagian plastik.
Pembuatan produk dimulai dengan desain. Desain komponen plastik secara langsung menentukan realisasi struktur internal, biaya dan fungsi produk, dan juga menentukan langkah selanjutnya dari produksi cetakan, biaya dan siklus, serta proses dan biaya pencetakan injeksi dan pasca-pemrosesan.
Komponen plastik banyak digunakan dalam berbagai produk, fasilitas, dan kehidupan masyarakat di masyarakat modern. Komponen plastik membutuhkan bentuk dan fungsi yang berbeda. Mereka menggunakan bahan plastik dan sifatnya bervariasi. Pada saat yang sama, banyak cara untuk membuat komponen plastik di industri. Jadi mendesain komponen plastik bukanlah pekerjaan yang mudah.
Desain dan bahan bagian yang berbeda menghasilkan pemrosesan yang berbeda. Pengolahan plastik cetakan terutama meliputi:
1. cetakan injeksi
2. meniup cetakan
3. cetakan kompresi
4. cetakan rotasi
5. bentuk lain
6. ekstrusi
7. fabrikasi
8. berbusa
Ada banyak cara untuk memproduksinya secara massal. Cetakan injeksi adalah metode manufaktur yang populer, karena cetakan injeksi 50% ~ 60% bagian plastik diproduksi oleh cetakan injeksi, ini adalah kemampuan produksi berkecepatan tinggi.
Tunjukkan case untuk beberapa bagian plastik yang kami rancang:
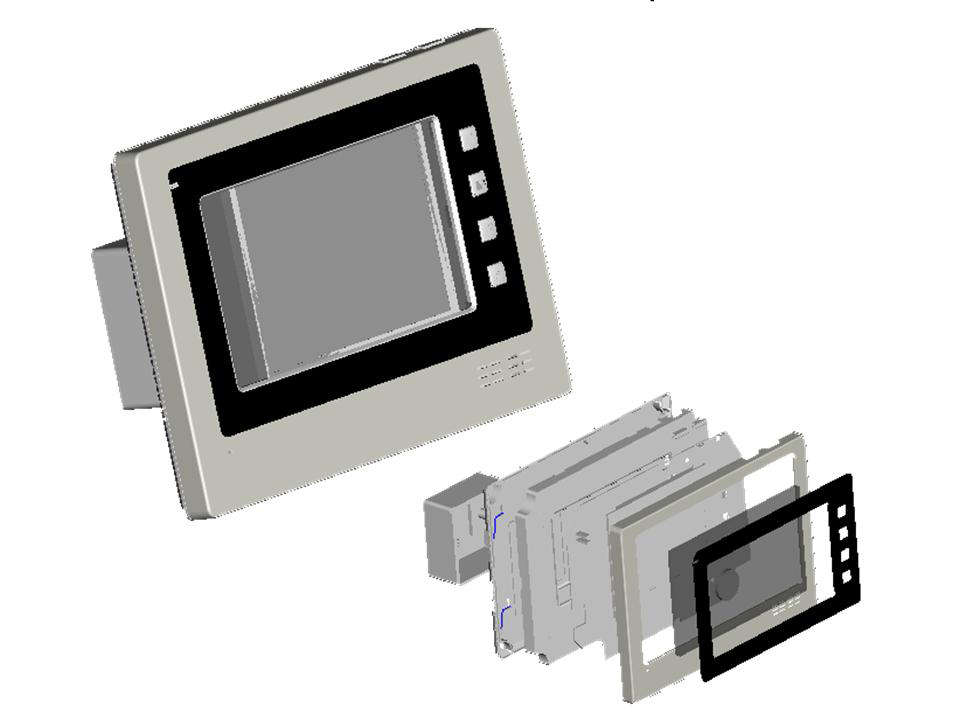
Kandang plastik telepon vision
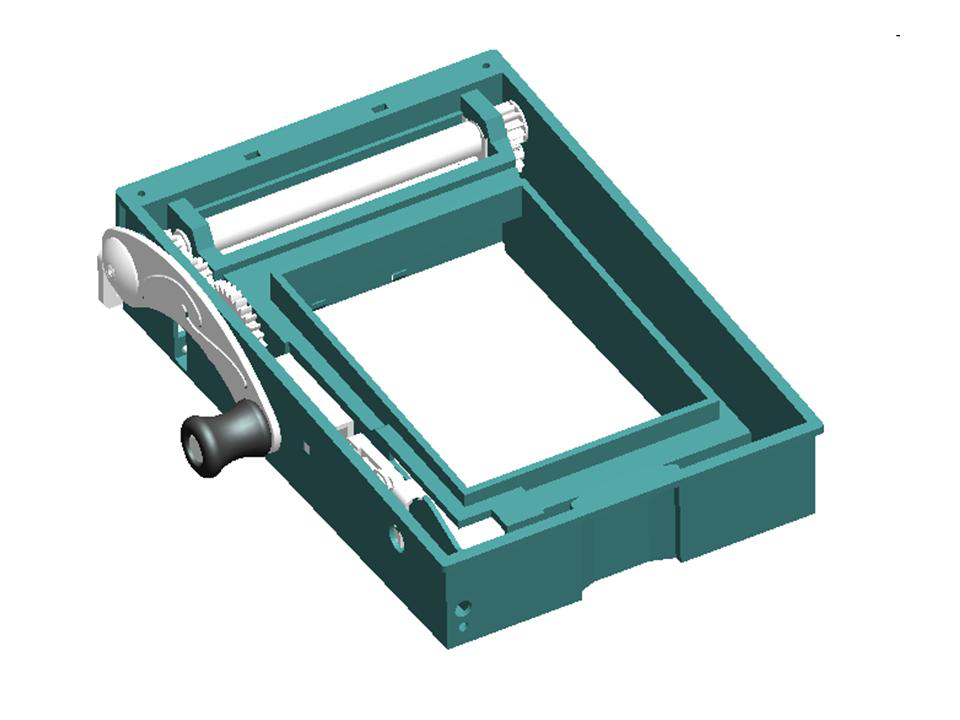
Mekanisme bagian plastik
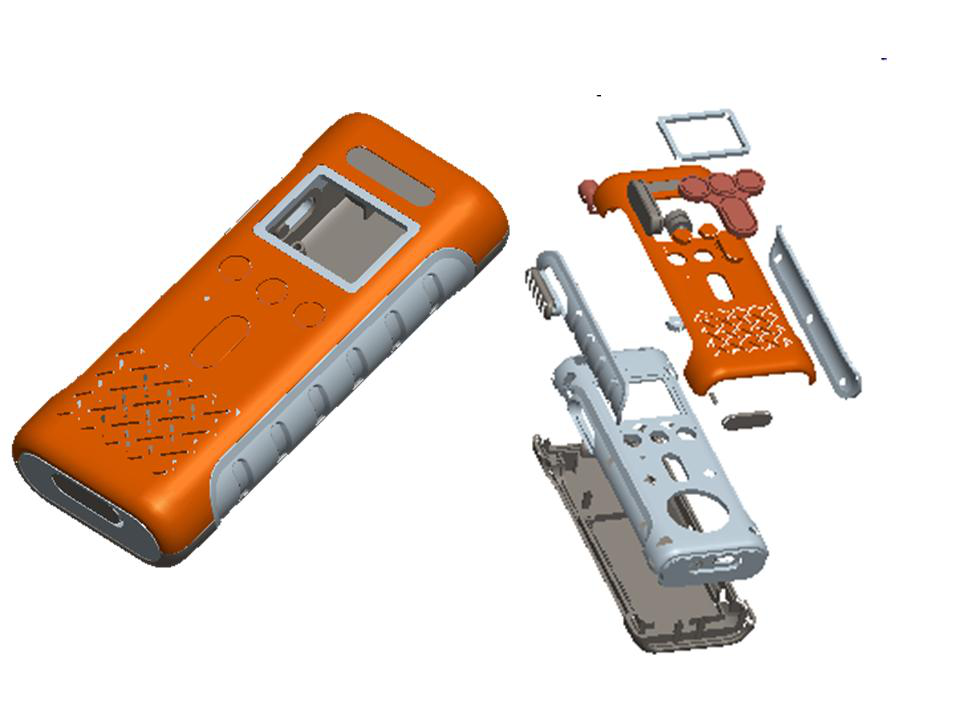
Kotak plastik elektronik
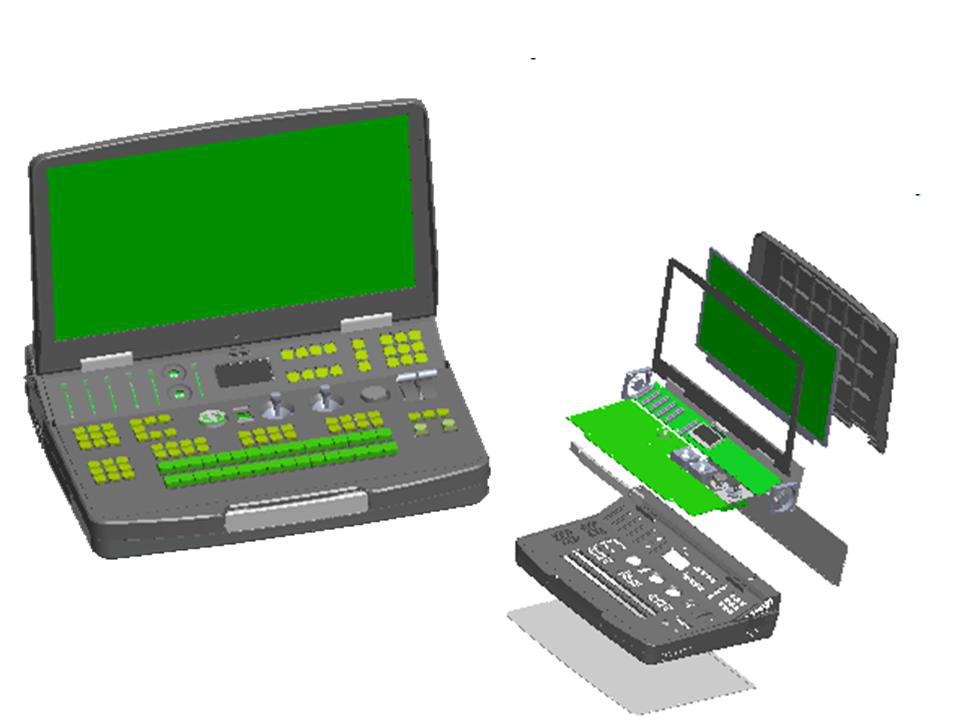
Rumah plastik untuk instrumen
Di bawah ini kami membagikan detail cara mendesain komponen plastik dalam tiga aspek
* 10 tips mendesain komponen plastik yang harus Anda ketahui
1. Tentukan desain penampilan dan ukuran produk.
Ini adalah langkah pertama dalam keseluruhan proses desain. Menurut riset pasar dan kebutuhan pelanggan, tentukan penampilan dan fungsi produk, dan rumuskan tugas pengembangan produk.
Sesuai dengan tugas pengembangan, tim pengembangan melakukan analisis kelayakan teknis dan teknologi untuk produk, dan membangun model tampilan 3D produk. Kemudian, menurut realisasi fungsi dan perakitan produk, bagian-bagian yang mungkin direncanakan.
2. Pisahkan masing-masing bagian dari gambar produk, pilih jenis resin plastik untuk bagian plastik
Langkah ini untuk memisahkan bagian-bagian dari model 3D yang diperoleh pada langkah sebelumnya dan mendesainnya sebagai individu. Menurut persyaratan fungsional suku cadang, pilih bahan baku plastik atau bahan perangkat keras yang sesuai. Misalnya, ABS biasanya digunakan di
cangkang, ABS / BC atau PC diharuskan memiliki sifat mekanik tertentu, bagian transparan seperti kap lampu, tiang lampu PMMA atau PC, roda gigi atau bagian aus POM atau Nylon.
Setelah memilih bahan bagian-bagiannya, desain detail dapat dimulai.
3. Tentukan sudut konsep
Sudut draf memungkinkan untuk mengeluarkan plastik dari cetakan. Tanpa sudut rancangan, bagian tersebut akan menawarkan hambatan yang signifikan karena gesekan selama pelepasan. Sudut konsep harus ada di bagian dalam dan luar bagian. Semakin dalam bagiannya, semakin besar sudut konsep. Aturan praktisnya adalah memiliki draft sudut 1 derajat per inci. Tidak memiliki sudut draf yang cukup dapat mengakibatkan goresan di sepanjang sisi bagian dan / atau tanda pin ejektor yang besar (lebih lanjut tentang ini nanti).
Sudut draft permukaan luar: Semakin dalam bagiannya, semakin besar sudut draftnya. Aturan praktisnya adalah memiliki draft sudut 1 derajat per inci. Tidak memiliki sudut draf yang cukup dapat mengakibatkan goresan di sepanjang sisi bagian dan / atau tanda pin ejektor yang besar (lebih lanjut tentang ini nanti).
Biasanya, agar permukaan tampak bagus, tekstur dibuat pada permukaan bagian. Dinding yang teksturnya kasar, gesekannya besar, dan tidak mudah dikeluarkan dari rongga, sehingga membutuhkan sudut gambar yang lebih besar. Tekstur yang lebih kasar, dibutuhkan sudut peregangan yang lebih besar.
4. Tentukan ketebalan dinding / ketebalan seragam
Cetakan bentuk padat tidak diinginkan dalam cetakan injeksi karena alasan berikut:
1). Waktu pendinginan sebanding dengan kuadrat ketebalan dinding. Waktu pendinginan yang lama untuk padatan akan mengalahkan ekonomi produksi massal. (konduktor panas yang buruk)
2). Bagian yang lebih tebal menyusut lebih dari bagian yang lebih tipis, dengan demikian menyebabkan penyusutan diferensial yang menghasilkan lengkungan atau tanda tenggelam, dll. (Karakteristik penyusutan plastik dan karakteristik pvT)
Oleh karena itu kami memiliki aturan dasar untuk desain bagian plastik; sejauh mungkin ketebalan dinding harus seragam atau konstan di seluruh bagian. Ketebalan dinding ini disebut tebal dinding nominal.
Jika terdapat bagian padat pada bagian tersebut, maka bagian tersebut harus dibuat berlubang dengan memasukkan inti. Ini harus memastikan ketebalan dinding yang seragam di sekitar inti.
3). Apa saja pertimbangan dalam menentukan ketebalan dinding?
Ini harus cukup tebal dan kaku untuk pekerjaan itu. Ketebalan dinding bisa 0,5 sampai 5mm.
Ini juga harus cukup tipis untuk mendinginkan lebih cepat, menghasilkan bobot bagian yang lebih rendah dan produktivitas yang lebih tinggi.
Setiap variasi ketebalan dinding harus dijaga seminimal mungkin.
Bagian plastik dengan ketebalan dinding yang bervariasi akan mengalami kecepatan pendinginan dan penyusutan yang berbeda. Dalam kasus seperti itu, mencapai toleransi yang dekat menjadi sangat sulit dan seringkali tidak mungkin. Jika variasi ketebalan dinding penting, transisi antara keduanya harus bertahap.
5. Desain koneksi antar bagian
Biasanya kita perlu menghubungkan dua cangkang bersama. Untuk membentuk ruang tertutup di antara mereka untuk menempatkan komponen internal (perakitan atau mekanisme PCB).
Jenis koneksi biasa:
1). Pengait jepret:
Sambungan snap hook biasanya digunakan pada produk berukuran kecil dan menengah. Ciri khasnya adalah kait jepret umumnya dipasang di tepi bagian, dan ukuran produk bisa dibuat lebih kecil. Saat dirakit langsung ditutup tanpa menggunakan alat bantu apapun seperti obeng, die las ultrasonik dan lain-lain. Kerugiannya adalah kait jepret dapat menyebabkan jamur lebih rumit. Mekanisme penggeser dan mekanisme pengangkat diperlukan untuk mewujudkan koneksi kait jepret dan meningkatkan biaya cetakan.
2). Sambungan sekrup:
Sambungan sekrup kokoh dan andal. Secara khusus, fiksasi sekrup + mur sangat andal dan tahan lama, memungkinkan beberapa pembongkaran tanpa retak. Sambungan sekrup cocok untuk produk dengan gaya penguncian yang besar dan beberapa pembongkaran. Kerugiannya adalah kolom sekrup membutuhkan lebih banyak ruang.
3). Bos pemasangan:
Pemasangan koneksi bos adalah untuk memperbaiki dua bagian dengan koordinasi yang erat antara bos dan lubang. Cara sambungan ini tidak cukup kuat untuk memungkinkan produk dibongkar. Kerugiannya adalah kekuatan penguncian akan berkurang seiring bertambahnya waktu pembongkaran.
4). Pengelasan ultrasonik:
Pengelasan ultrasonik adalah dengan meletakkan dua bagian ke dalam cetakan ultrasonik dan menyatukan permukaan kontak di bawah aksi mesin las ultrasonik. Ukuran produk bisa lebih kecil, cetakan injeksi relatif sederhana, dan koneksinya kuat. Kerugiannya adalah penggunaan cetakan ultrasonik dan mesin las ultrasonik, ukuran produk tidak bisa terlalu besar. Setelah dibongkar, bagian ultrasonik tidak dapat digunakan kembali.
6. Jalan pintas
Pemotongan adalah item yang mengganggu pengangkatan salah satu setengah dari cetakan. Pemotongan dapat muncul di mana saja dalam desain. Ini sama tidak dapat diterima, jika tidak lebih buruk dari kurangnya sudut konsep pada bagian tersebut. Namun, beberapa pemotongan diperlukan dan / atau tidak dapat dihindari. Dalam hal itu, perlu
undercut diproduksi dengan menggeser / memindahkan bagian dalam cetakan.
Perlu diingat bahwa membuat potongan lebih mahal saat memproduksi cetakan dan harus diminimalkan.
7. Dukungan Ribs / Gussets
Rusuk di bagian plastik meningkatkan kekakuan (hubungan antara beban dan defleksi bagian) bagian tersebut dan meningkatkan kekakuan. Ini juga meningkatkan kemampuan cetakan karena mempercepat aliran leleh ke arah tulang rusuk.
Rusuk ditempatkan di sepanjang arah tegangan dan defleksi maksimum pada permukaan bagian yang tidak terlihat. Pengisian cetakan, penyusutan dan pengeluaran juga harus mempengaruhi keputusan penempatan tulang rusuk.
Iga yang tidak menyatu dengan dinding vertikal sebaiknya tidak putus tiba-tiba. Transisi bertahap ke dinding nominal akan mengurangi risiko konsentrasi stres.
Rib - dimensi
Tulang rusuk harus memiliki dimensi berikut.
Ketebalan rusuk harus antara 0,5 sampai 0,6 kali ketebalan dinding nominal untuk menghindari tanda tenggelam.
Tinggi rusuk harus 2,5 sampai 3 kali ketebalan dinding nominal.
Rib harus memiliki sudut draft 0,5 hingga 1,5 derajat untuk memfasilitasi pengeluaran.
Basis rusuk harus memiliki radius 0,25 hingga 0,4 kali ketebalan dinding nominal.
Jarak antara dua tulang rusuk harus 2 hingga 3 kali (atau lebih) ketebalan dinding nominal.
8. Tepi Radius
Ketika dua permukaan bertemu, itu membentuk sudut. Di sudut, ketebalan dinding bertambah menjadi 1,4 kali lipat ketebalan dinding nominal. Hal ini menghasilkan penyusutan yang berbeda dan tegangan yang terbentuk serta waktu pendinginan yang lebih lama. Oleh karena itu, risiko kegagalan layanan meningkat di tikungan tajam.
Untuk mengatasi masalah ini, sudut harus dihaluskan dengan jari-jari. Radius harus disediakan secara eksternal maupun internal. Tidak pernah memiliki sudut tajam internal karena mempromosikan retakan. Radius harus sedemikian rupa sehingga sesuai dengan aturan ketebalan dinding yang konstan. Diutamakan yang memiliki radius 0,6 sampai 0,75 kali ketebalan dinding pada sudut-sudutnya. Tidak pernah memiliki sudut tajam internal karena mempromosikan retakan.
9. Desain bos sekrup
Kami selalu menggunakan sekrup untuk memperbaiki dua setengah casing, atau mengencangkan PCBA atau komponen lain ke bagian plastik. Jadi bos sekrup adalah struktur untuk mengencangkan dan memperbaiki bagian.
Bos sekrup berbentuk silinder. Bos mungkin ditautkan di pangkalan dengan bagian ibu atau mungkin ditautkan di samping. Menghubungkan ke samping dapat mengakibatkan bagian plastik yang tebal, yang tidak diinginkan karena dapat menyebabkan tanda tenggelam dan meningkatkan waktu pendinginan. Masalah ini dapat diatasi dengan menghubungkan bos melalui rusuk ke dinding samping seperti yang ditunjukkan pada sketsa. Atasan bisa dibuat kaku dengan memberikan tulang rusuk penopang.
Sekrup digunakan pada bos untuk mengikat beberapa bagian lainnya. Ada jenis sekrup pembentuk ulir dan jenis sekrup pemotongan tapak. Sekrup pembentuk ulir digunakan pada termoplastik dan sekrup pemotong ulir digunakan pada bagian plastik termoset yang tidak elastis.
Sekrup pembentuk ulir menghasilkan ulir betina di dinding bagian dalam bos dengan aliran dingin - plastik dideformasi secara lokal daripada dipotong.
Bos sekrup harus memiliki dimensi yang tepat untuk menahan gaya penyisipan sekrup dan beban yang ditempatkan pada sekrup yang berfungsi.
Ukuran lubang relatif terhadap sekrup sangat penting untuk ketahanan terhadap pengupasan ulir dan penarikan sekrup.
Diameter luar bos harus cukup besar untuk menahan tekanan lingkaran akibat pembentukan benang.
Lubang memiliki diameter yang sedikit lebih besar pada ceruk masuk dengan panjang yang pendek. Ini membantu dalam menemukan sekrup sebelum masuk. Ini juga mengurangi tekanan pada ujung terbuka bos.
Produsen polimer memberikan pedoman untuk menentukan dimensi atasan untuk bahan mereka. Produsen sekrup juga memberikan pedoman untuk ukuran lubang yang tepat untuk sekrup tersebut.
Perhatian harus diberikan untuk memastikan sambungan las yang kuat di sekitar lubang sekrup di bos.
Perhatian harus diberikan untuk menghindari stres yang membur pada bos karena dapat gagal di bawah lingkungan yang agresif.
Bore in boss harus lebih dalam dari kedalaman benang.
10. Dekorasi permukaan
Terkadang, untuk mendapatkan tampilan yang menarik, kami sering melakukan perawatan khusus pada permukaan casing plastik.
Seperti: tekstur, glossy tinggi, lukisan semprot, ukiran laser, hot stamping, pelapisan listrik dan sebagainya. Hal ini perlu diperhatikan dalam desain produk terlebih dahulu, untuk menghindari proses selanjutnya tidak dapat dicapai atau perubahan ukuran yang mempengaruhi perakitan produk.